概要
発生元と発生状況
石炭灰(クリンカアッシュ+フライアッシュ)は、主に石炭火力発電ボイラーで石炭(微粉炭)を燃焼させた際に発生する副産物です。日本国内では、平成27年度に1,272万t(電気事業934万t、一般産業338万t)の石炭灰が発生しており、うち1,247万tが有効利用されています(有効利用率98.0%)。なお、一般産業としては、化学工業、製紙業、IPP・PPS※、窯業土石、鉄鋼業が主に挙げられます。
※IPP:独立系発電事業者、PPS:特定規模電気事業者
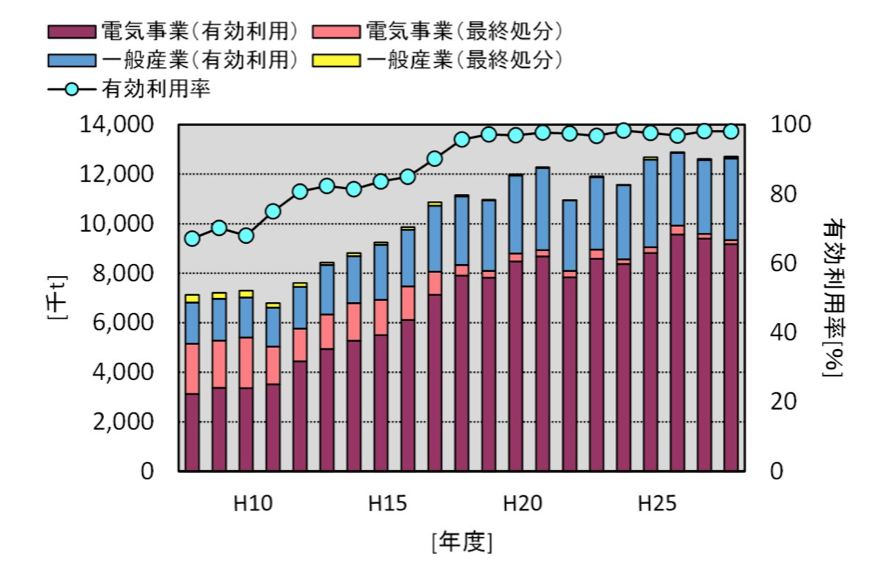
(出典:平成28年度石炭灰全国実態調査報告書(平成27年度))
平成27年度石炭使用量に対する石炭灰の発生割合は平均11.2%であり、電気事業は11.0%、一般産業は11.9%となっております。
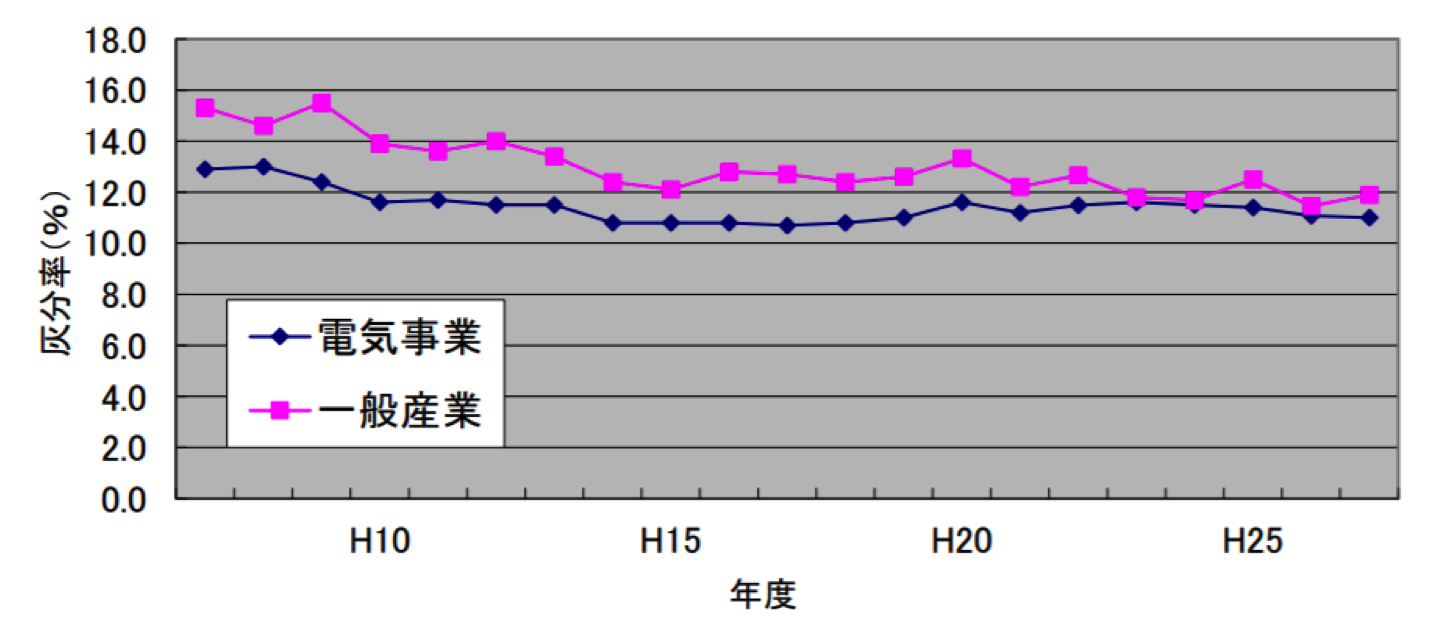
(出典:平成28年度石炭灰全国実態調査報告書(平成27年度))
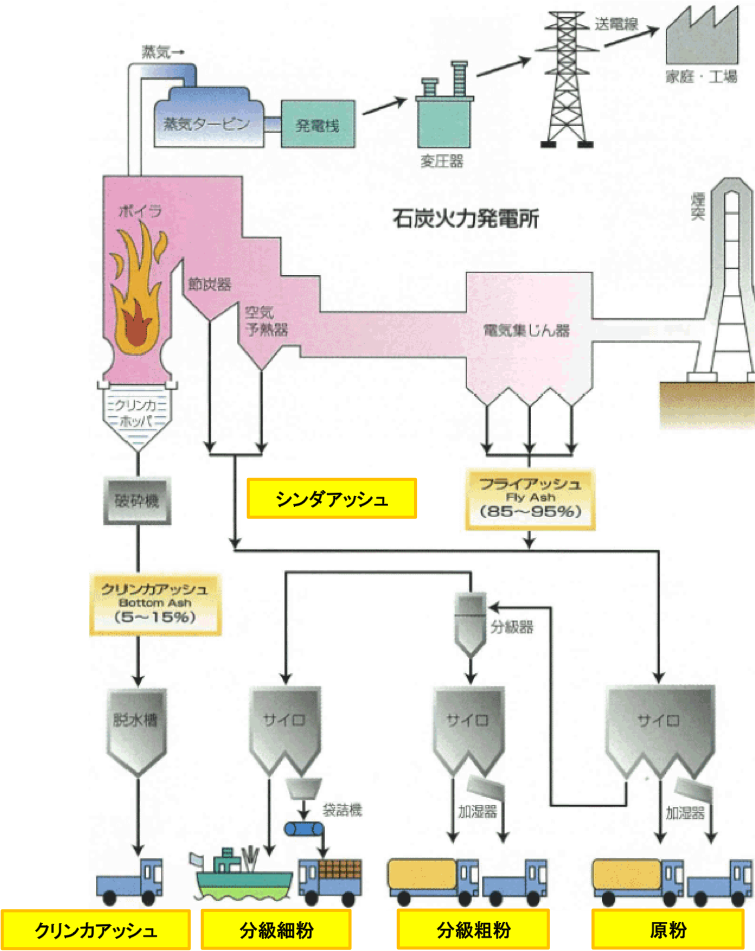
(出典:日本フライアッシュ協会のホームページ)
石炭火力発電所で使用されるボイラとしては流動床ボイラもありますが、ここでは微粉炭ボイラを対象とします。
微粉炭ボイラでは、微粉炭を燃焼させたあとの残渣として石炭灰が発生します。発生箇所により、ボイラ炉底から採取されるクリンカアッシュ(砂状)、節炭器・空気予熱器から採取されるシンダアッシュ(粉状)、および集じん器から採取されるフライアッシュ(粉状)に分けられます。
フライアッシュとシンダアッシュは共にサイロに収集された後、気流分級器によって分級されます。分級細粉は粒の細かいフライアッシュ、粗粉はシンダアッシュや粒の粗いフライアッシュを集めたものです。
なお、石炭灰のうち85~95%がフライアッシュとして回収され、5~15%がクリンカアッシュとして回収されます。
<CO2削減効果:フライアッシュのセメント混合材コンクリート混和材としての利用>
- セメントは、石灰石(炭酸カルシウムCaCO3)等原材料を1450℃程度で焼成後粉砕し製造され輸送され利用されます。この焼成・粉砕・輸送に要する燃料等から発生するCO2と、焼成の際に石灰石から発生する脱炭酸分CO2と合わせ、セメント1tを使用する際には約760kgのCO2が発生します。
- 一方、フライアッシュは副産物であることから製造に関わるCO2は非常に少なく、主に輸送の際に発生するCO2を考慮することになり、フライアッシュ1tを使用する際に発生するCO2は約20kgと、セメントに比べ排出量が非常に少量です。
- このため、フライアッシュをセメント混合材やコンクリート混和材として使用し、セメント使用量を低減しますと、より少ないCO2排出量でコンクリートを製造することが出来ます。
- 例として、同じ配合でコンクリートを製造する場合、フライアッシュセメントB種を使用することによって、普通セメントを使用した場合に比べCO2排出量を約20%低減することが出来ます。このように、フライアッシュのコンクリートへの利用は環境面で優れています。
セメントのインベントリデータ(CO2排出量)
セメント種類 | CO2排出量(kg-CO2/t) |
---|---|
普通セメント | 765.5 |
フライアッシュセメントB種 | 622.8 |
(出典:コンクリート技術シリーズ62
コンクリートの環境負荷評価(その2)
公益社団法人土木学会)